Bei hochkomplexen Anwendungen, wo andere MMS-Systeme schon frühzeitig die Flügel streckten, spielt das 2015 vorgestellte MMS-System Controlube seine Stärken aus. Durch variabel einspritzbare Ölmengen, Luftdrücke bis 20 bar und eine spezielle Mikroprozessor-Steuerung eignet es sich sogar, um bei Modulmaschinen über 90 Werkzeuge optimiert mit Minimalmengenschmierung zu versorgen. Für ein breiteres Anwendungsfeld, das keine derartige High-End-Ausstattung benötigt, war Controlube bislang aber schlichtweg zu teuer. Um im Midrange-Markt nicht „mit Kanonen auf Spatzen schießen“ zu müssen, gestaltete Knoll sein MMS-System für einen bedarfsgerechten Einsatz um: Ein modularer Aufbau hält alle systembedingten Vorteile aufrecht und lässt eine bedarfsgerechte Konfiguration zu.
Bei Controlube kann die Ölmenge unabhängig von der eingesetzten Luftmenge variiert werden. Dafür ist das Injektorprinzip verantwortlich, das von der Kraftstoffeinspritzung im Automobil bekannt ist. Öl und Druckluft werden separat zu einer Mischkammer geführt, die sich kurz vor der Spindel-Drehdurchführung befindet. Ein Injektor spritzt das Öl in einer frei wählbaren Menge von bis zu 400 ml/h unter Hochdruck von 600 bar ein. Es vermischt sich mit der – im Basismodul unter Hallendruck (also etwa 4 bis 5 bar) – zugeführten Luft zu einem sehr feinen Aerosol, dessen Ölpartikel eine Größe von etwa 0,3 µm haben. Das stark komprimierte Luft-/Öl-Gemisch wird anschließend durch die Spindel zum Werkzeug geführt, wo es nach sehr kurzer Reaktionszeit von unter 0,1 s zur Verfügung steht.
Bei vergleichbaren MMS-Systemen, die nach dem Venturi-Prinzip arbeiten, gilt dagegen: Je mehr Öl benötigt wird, desto mehr Luft muss eingesetzt werden, um das Öl zu transportieren. Bei Planfräsern zum Beispiel entstehen dadurch unnötige Kosten. Denn diese Werkzeuge benötigen zwar eine große Ölmenge, aber nur wenig Luft zum Entfernen der Späne. Dazu kommt, dass der Einsatz einer Venturi-Düse zwangsläufig mit einem Druckabfall von etwa 2 bar verbunden ist. Ein Umstand, der bei der Injektortechnik nicht auftritt: Hier kommt der eingesetzte Luftdruck nach der Drehdurchführung auch vorne am Werkzeug an.
Mit Modulen zur bedarfsgerechten MMS-Anlage
Das Controlube-Basismodul bietet 26 verschiedene Ölprogramme und einen integrierten 15-Liter-Öltank. Bis zu acht Mischkammern lassen sich anschließen, um mehrspindlige Anlagen oder mehrere Maschinen zu versorgen. Eine Montageplatte ermöglicht die flexible Integration. Ergänzend bietet der Hersteller Module an, die der Anwender auch nachträglich per Plug & Play installieren kann. Stellt er zum Beispiel fest, dass er für spezielle Anwendungen (Tieflochbohren oder den Einsatz sehr kleiner Werkzeuge) einen höheren Luftdruck benötigt, um die Späne aus der Bearbeitungszone zu entfernen, wählt er nach Bedarf eines von zwei Druckerhöhungsmodulen aus, die Druckluft mit 10 oder 20 bar erzeugen und über ein die Effizienz steigerndes Schaltventil verfügen. Der Ausgangsdruck ist manuell einstellbar.
Für eine automatische Druck- und Mengenregelung mit Festwerten oder Variablen steht das Regelmodul „Pro“ zur Verfügung. Mit ihm lässt sich der Luftdruck je nach Druckstufe zwischen 0 und 20 bar fast stufenlos im Kommabereich frei regeln. Die zugeführte Ölmenge kann automatisch in ml-Schritten von 0 bis 400 ml/h variiert werden. Das Regelmodul nutzt eine speziell entwickelte Elektronik auf Mikroprozessor-Basis, die für kurze Reaktionszeiten bei Programmwechsel sowie Zyklusbetrieb sorgt und die Möglichkeit zum Live-Monitoring bietet. Sie ist über Profinet oder ein anderes Bussystem mit der CNC-Werkzeugmaschine verbunden.
Knoll Maschinenbau GmbH
www.knoll-mb.de
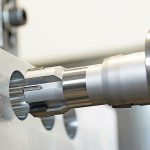
Vorteil MMS
Branchen wie die Luftfahrt- und Automobilindustrie, die Werkstücke aus Aluminium-, Knet- und Gusslegierungen, Grauguss, Stählen und rostfreiem Material in großen Stückzahlen produzieren, setzen immer häufiger Minimalmengenschmierung (MMS) ein. Denn allein aus der geringen Menge benötigten Schmierstoffs ergeben sich zahlreiche Vorteile. Der Volumenstrom bei MMS liegt in der Regel bei weniger als 50 ml pro Stunde, während bei der Nass-Kühlschmierung in der gleichen Zeit bis zu 12 000 Liter eingesetzt werden. So spart der Anwender sowohl beim Verbrauch als auch bei der Überwachung und Pflege sowie der Aufbereitung bzw. Entsorgung, denn die minimalen Mengen Schmierstoff verdampfen bei optimalem Prozess nahezu rückstandslos.
Für viele Anwendungen sind die durch MMS entstehenden Prozessvorteile noch entscheidender. Bei der Zerspanung mit Nass-Kühlschmierung bleiben Feinstpartikel in Öl und Emulsion zurück, die bei der Wiederverwendung die Oberflächenqualität gefährden und dementsprechend aufwändig herausgefiltert werden müssen. Dieses Problem gibt es bei MMS nicht. Der eingesetzte Schmierstoff wird komplett verbraucht und daher stets neu in reiner Qualität zugeführt.
Zudem profitiert der Anwender von geringerem Werkzeugverschleiß, der auf die bessere Schmierung und geringere Thermoschockwirkung (bei unterbrochenem Schnitt) zurückzuführen ist. Auch lassen sich bei idealen Bedingungen höhere Werkzeugvorschübe realisieren. Nicht zuletzt gehören der geringere Platzbedarf, der niedrigere Geräuschpegel und weniger Gesundheitsgefahren für den Bediener zu den positiven Seiten der MMS.
Hier finden Sie mehr über: